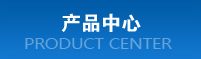

車床改旋壓機的方法_羅茨風機
車床改旋壓機的方法:一種強力旋壓機復合旋壓用旋輪的制作方法
本實用新型屬于旋壓技術領域,涉及一種強力旋壓機復合旋壓用旋輪。
背景技術:
旋壓技術是一種金屬近凈成形工藝,尤其對于回轉體類零件其工裝模具需求簡單,因此近年來在航天航空領域應用越來越多。旋壓機旋壓時,根據(jù)旋壓工藝的不同一般需要應用到不同形狀的旋輪,其內形由設備的連接方式決定,其外形(旋輪的工作直徑、工作角、工作型面等)則基于對旋壓變型的考慮。一般在旋壓時在確保滿足旋壓件旋壓的前提下應盡可能選用結構簡單的旋輪,但一般一種零件在旋壓時可能要采用幾種不同性質的旋壓工藝才能完成,而不同旋壓工藝所應用的旋輪工作型面又不相同,這樣就需要分工序采用不同的旋壓方法,比如先普通旋壓再強力旋壓減薄,有的零件可能需要在一道旋壓工序中就有兩種不同的旋壓工藝,即普旋強旋同時進行,例如對厚底薄壁類桶形件的旋壓就采用這種工藝。如果根據(jù)旋壓工藝要求對于厚底薄壁類零件旋壓時一般需要更換旋輪才能很好的保證產品質量,但更換旋輪來保證產品質量的做法缺點是:需要多個(對)不同型面的旋輪,工裝費用高;需要設備停機更換導致加工時間長。
技術實現(xiàn)要素:
本實用新型的目的在于克服上述現(xiàn)有技術的缺點,提供一種強力旋壓機復合旋壓用旋輪,該旋輪型面上存在兩個用于普通旋壓和強力旋壓用型面,用來復合旋壓時工序少,節(jié)省了加工時間。
本實用新型的目的是通過以下技術方案來實現(xiàn)的:
一種強力旋壓機復合旋壓用旋輪,包括用于對板坯進行普通旋壓和強力旋壓的旋輪,所述旋輪的工作型面包括相連的三部分,分別是用于普旋的圓型面、15~30°的錐形型面、退出角部分,其中,用于普旋的圓型面的半徑大于錐形型面的半徑。
本實用新型進一步的改進在于,錐形型面與用于普旋的圓型面、退出角部分連接處以圓弧過渡。
本實用新型進一步的改進在于,板坯厚度為t0時,用于普旋的圓型面的半徑為t0的1~5倍。
本實用新型進一步的改進在于,板坯厚度為2~6mm時,用于普旋的圓型面的半徑為12mm。
本實用新型進一步的改進在于,板坯厚度為2~6mm時,退出角部分的半徑為12mm。
本實用新型進一步的改進在于,板坯厚度為2~6mm時,圓弧半徑為5mm。
與現(xiàn)有技術相比,本實用新型的有益效果:
本實用新型的旋輪用于普通旋壓和強力旋壓需要同時進行的場合,旋輪型面包括用于普旋的圓型面和用于強旋的錐形型面,存在兩個不同大小的R,較大的R型面專門針對普旋成型,較小的R及錐形型面針對強力旋壓減薄階段的成型,而不必再更換旋輪進行復合旋壓,可以對圓板形坯料通過復合旋壓(普通旋壓,強力旋壓依次或交替旋壓的工藝),與普通的單一型面旋輪旋壓相比具有旋壓工序少,節(jié)省加工時間等優(yōu)勢。
附圖說明
圖1為本實用新型的強力旋壓機復合旋壓用旋輪示意圖。
圖2為復合旋壓過程中旋輪工作情況示意圖。
具體實施方式
下面結合附圖對本實用新型做進一步描述:
如圖1所示,本實用新型包括旋輪,旋輪的工作型面4包括三部分,分別是用于普旋的型面1、15~30°的錐形型面2、退出角部分3,其中,板坯厚度為2~6mm時,錐形型面與退出角部分交界處以半徑為5mm的圓弧過渡。普旋的型面1的半徑為12mm,退出角部分3的半徑為12mm。15~30°的錐形型面2的形成可以看做是將旋輪頂端沿一側去除一部分,即呈圓形,并且去除該部分后的型面與旋輪頂端切面方向的夾角為15~30°。
本實用新型是一種適合板坯厚度為2~6mm的普旋+強旋復合旋壓用旋輪,該旋輪以普通旋壓用標準圓形型面旋輪為基礎,普通旋壓用標準圓形旋輪工作型面部分半徑為R,圖1中左半部分R12部分用于普通旋壓,將前端用于強力旋壓部分設計成15~30°錐形型面,與退出角R12交界處以R5圓弧過渡,形成強力旋壓工作型面4。在進行以圓板形坯料旋壓厚底薄壁桶形件時,壁部減薄部分主要使用15~30°工作角、R5、R12退出壓光,而圓板旋壓成桶形的過程主要使用R12型面普旋成型。
以下給出本實用新型強力旋壓機復合旋壓用旋輪的設計原則:
1)根據(jù)旋壓機采用的圓形型面標準旋輪的大小設計,該復合旋壓用旋輪,除工作型面外,其余部分結構、旋輪用材料等均與其他標準旋輪相同;
2)工作型面普旋部分,根據(jù)要進行旋壓的圓形板料毛坯厚度確定普通旋壓部分型面R大小,原則上旋輪工作圓弧半徑R為(1~5)t0(t0—毛坯厚度),即工作圓弧半徑R為圓形板料毛坯厚度的1~5倍。
3)工作型面強旋部分,實際生產中工作角經驗數(shù)據(jù)可以取15~30°,材料相對較軟時,比如鋁、銅或退火態(tài)材料可以取較小值,材料較硬時,比如不銹鋼、高溫合金、鈦合金等可以取較大值。退出角R與工作角的圓弧過渡部分為主要工作面,針對強力旋壓減薄時,旋輪的工作圓弧半徑R一般為(0.4~1)t0(t0—毛坯厚度),為了提高強旋減薄時旋輪的使用壽命,也可將旋輪的工作圓弧半徑R提高為(0.85~1.75)t0,退出角R部分選擇與普旋部分相同,主要對工件起到壓光作用。
旋壓時,如圖2所示,將待加工的工件6設置模具7上,下半部分為最初進行普通旋壓時,旋輪普旋部分型面為主要工作面;圖2中上半部分為普旋強旋同時進行時,強旋部分型面為主要工作面。旋輪的所有工作型面完全符合旋壓過程的工藝要求,在普旋和強旋需要同時進行時不再需要更換旋輪便能達到最佳的旋壓效果。
本實用新型的旋輪用于普通旋壓和強力旋壓需要同時進行的場合,旋輪型面上存在兩個不同大小的R,較大的R型面可以專門針對普旋成型,較小的R及錐形面針對強力旋壓減薄階段的成型,而不必再更換旋輪進行旋壓。該旋輪主要用于普通旋壓后需要強力旋壓減薄延長的情況。
車床改旋壓機的方法:一種數(shù)控旋壓機的制作方法
本實用新型涉及一種數(shù)控旋壓機。
背景技術:
金屬旋壓是一種金屬塑性成形的加工工藝,它通過旋輪做進給運動,加壓于隨芯模沿同一軸線旋轉的圓形板坯料,使其產生連續(xù)局部塑性變形,成為所需零件的先進成形方法,是一種無切削加工工藝,具有快捷、省力、節(jié)能、精度高、表面質量好、材料利用率高、生產成本低和應用范圍廣等優(yōu)點。
此外,前市面上的數(shù)控旋壓機,一般都是用耐磨耐高溫膠刀輪作為旋壓刀,這種膠刀輪的缺點是成本高,易磨損,使用壽命短,而且對旋壓的工藝要求較高,如對刀輪跳動、模具跳動和尾頂跳動等技術要求較高,并且現(xiàn)有的數(shù)控旋壓機工作范圍較小,同時,現(xiàn)有的數(shù)控旋壓機刀架裝卸刀刃不方便,且兼容性較差,并且旋壓的產品的精度較低,生產效率低,局限性大。
技術實現(xiàn)要素:
本實用新型要解決的技術問題是提供一種工作效率高、智能操控和自動化程度高的數(shù)控旋壓機。
為解決上述問題,本實用新型采用如下技術方案:
一種數(shù)控旋壓機,包括數(shù)控裝置和旋壓機床,所述數(shù)控裝置位于旋壓機床的左側,所述數(shù)控裝置與旋壓機床相連接,所述旋壓機床的左端設置有主軸卡盤,所述主軸卡盤上固定有旋壓模,所述旋壓模上設置有工件,所述旋壓機床的中部設置有橫向油缸,所述橫向油缸的下端設置有橫向拖板,所述旋壓機床的右下方設置有縱向油缸,所述縱向油缸的左端設置有縱向拖板,所述旋壓機床的右端設置有尾座,所述尾座上設置有尾頂氣缸,所述尾頂氣缸與尾座相固定。
作為優(yōu)選,所述數(shù)控裝置內設置有PLC控制器,有利于控制旋壓機床的運作。
作為優(yōu)選,所述旋壓模的右端為半圓設置,有利于旋壓的力度集中在一點,便于對工件進行旋壓。
作為優(yōu)選,所述橫向油缸位于縱向拖板內,有利于在收緊時使得橫向油缸和縱向油缸相固定。
作為優(yōu)選,所述縱向油缸的左端設置有驅動桿,有利于驅動縱向拖板移動。
作為優(yōu)選,所述尾頂氣缸的左端設置有頂塊。
作為優(yōu)選,所述頂塊與工件相固定,有利于固定工件,并防止工件在旋壓過程中出現(xiàn)偏移。
本實用新型的有益效果為:由于設置有數(shù)控裝置,能夠輸入編程,并通過編程控制旋壓機床運作,由于設置有旋壓模,能夠在主軸卡盤的驅動下對工件進行旋壓成型,由于設置有橫向油缸和縱向油缸,有利于工件固定,由于設置有尾座,能夠通過尾座的尾頂氣缸對工件進行固定,有利于防止工件旋壓時出現(xiàn)位置偏移,進而造成工件損壞。
附圖說明
圖1為本實用新型一種數(shù)控旋壓機的整體結構示意圖。
具體實施方式
如圖1所示,一種數(shù)控旋壓機,包括數(shù)控裝置1和旋壓機床2,所述數(shù)控裝置1位于旋壓機床2的左側,所述數(shù)控裝置1與旋壓機床2相連接,所述旋壓機床2的左端設置有主軸卡盤3,所述主軸卡盤3上固定有旋壓模4,所述旋壓模4上設置有工件5,所述旋壓機床2的中部設置有橫向油缸6,所述橫向油缸6的下端設置有橫向拖板7,所述旋壓機床2的右下方設置有縱向油缸8,所述縱向油缸8的左端設置有縱向拖板9,所述旋壓機床2的右端設置有尾座10,所述尾座10上設置有尾頂氣缸11,所述尾頂氣缸11與尾座10相固定。
所述數(shù)控裝置1內設置有PLC控制器(未圖示),有利于控制旋壓機床1的運作。
所述旋壓模4的右端為半圓設置,有利于旋壓的力度集中在一點,便于對工件進行旋壓,
所述橫向油缸6位于縱向拖板9內,有利于在收緊時使得橫向油缸6和縱向油缸8相固定。
所述縱向油缸8的左端設置有驅動桿,有利于驅動縱向拖板9移動。
所述尾頂氣缸11的左端設置有頂塊。
所述頂塊與工件5相固定,有利于固定工件5,并防止工件5在旋壓過程中出現(xiàn)偏移。
本實用新型的有益效果為:由于設置有數(shù)控裝置,能夠輸入編程,并通過編程控制旋壓機床運作,由于設置有旋壓模,能夠在主軸卡盤的驅動下對工件進行旋壓成型,由于設置有橫向油缸和縱向油缸,有利于工件固定,由于設置有尾座,能夠通過尾座的尾頂氣缸對工件進行固定,有利于防止工件旋壓時出現(xiàn)位置偏移,進而造成工件損壞。
以上所述,僅為本實用新型的具體實施方式,但本實用新型的保護范圍并不局限于此,任何不經過創(chuàng)造性勞動想到的變化或替換,都應涵蓋在本實用新型的保護范圍之內。
車床改旋壓機的方法:供應普通車床改造為數(shù)控旋壓機
普通車床改造為數(shù)控旋壓機
數(shù)控旋壓機床相比普通液控旋壓機,不僅可以減輕勞動強度,提高旋壓產品的生產效率和成品率,而且還可以成形高精度、形狀復雜的旋壓產品。
由于數(shù)控旋壓設備價格高,且有進口依賴,而普通車床改造成數(shù)控旋壓機具有投資少、控制穩(wěn)定、適合專用旋壓技術等特點,具有極大的經濟效益和社會效益。
將普通車床改造為數(shù)控旋壓機,涉及到強度剛度設計、機械結構設計、液壓系統(tǒng)設計、數(shù)控系統(tǒng)設計及其安裝調試等關鍵技術,我公司擁有強大的專業(yè)技術團隊和多個成功改造實例(旋壓工件直徑從0.3米到3.5米均有),能滿足有特殊要求的用戶或者使用經驗不足的用戶需求。穩(wěn)定的改造成果及良好的信譽已贏得了業(yè)界良好的聲譽和認可。
業(yè)務范圍:
可根據(jù)客戶要求定制改造其它各類旋壓機床
承接旋壓設備維修、改造及升級換代工程
提供數(shù)控旋壓全套的解決方案。
普通車床改造成為數(shù)控旋壓機
車床改旋壓機的方法:自動旋壓機的總體布局設計思維指導
自動旋壓機的總體布局設計思維指導
結全之前我司網(wǎng)站公布的技術文章,我們日常在自動旋壓機的總體布局設計思維方面主要取決于自動旋壓機的用途和旋壓件的工藝過程中。通常在考慮旋壓機的布局時,可參照以下指導方法:
1.滿足自動旋壓機旋壓件的工藝要求
自動旋壓機的布局方式首先應該滿足工藝要求。一般來說,不同旋壓法決定了所需的成形運動。也就決定了各主要部件的相互關系,旋壓機的布局就應首先滿足這些已給定的工藝要求。由于專用旋壓機的工藝過程較為簡單,所需要考慮的因素也較少;對于通用型旋壓機則應考慮各種可能的加工要求。例如筒形件或管材強力旋壓機,只要求幾個旋輪布置在工件的周圍上,并可作橫向和縱向同步進給。一般是把這幾個旋輪等分地布置在一個剛性框架上,可免去縱向進給同步的問題;封頭旋壓和氣瓶收口或封底旋壓,則要求一個或兩個旋輪布置在工件的一側或兩側作帶橫向進給的圓弧擺動;對于既要加工錐形件、筒形件,又要加工復合形零件的通用型自動旋壓機,則要求一個或兩個旋輪布置在主軸軸線一側或兩側,且要求旋輪不但作橫向和縱向進給,還要作圓周轉角調整。以適應工藝上改變旋輪攻角的要求。此外,由前述可知,旋壓法是多種多樣的,它們也對設備結構布局產生各不相同的影響,例如中小直徑管材旋壓機由于工件和芯模較小,一般把旋輪布置在管子的外圓周,并采取芯模和管子轉動的方式,因而這種管材強力旋壓機,由于芯模較大、特重和制造困難等原因,就采取內旋壓法,即把芯模制成固定環(huán)形的,管坯置入環(huán)形模內,旋輪及其支架作旋轉運動和軸向進給,這兩種旋壓機在布局和外形上就完全不同了。
對于具有完整工藝流程的旋壓機布局,還要考慮工件的流程順序,從毛坯來源、上料對中和裝夾、旋壓、卸下工件、輸送到必要的中間工序(如退火、酸洗和整形等)及進一步加工(如再次旋壓、機械加工、焊接和涂層等),直至成品輸送、收集保存或輸送到自動線的下一工序中去。在考慮整個工藝流程的設備布局時,還應注意工件的流動方向對其布局的影響。
2.處理好自動旋壓機旋壓件加工范圍的寬窄
由上述可知,一臺旋壓機的加工對像與加工要求對其選型與結構關系很大。如果把多種多樣的產品都放在一臺旋壓機上加工,即要求旋壓機是“萬能”型的。這種加工范圍寬的旋壓機即使可以設計和制造出來,但往往存在性能差、精度低,成本高和使用不便等缺點,尤其是大型旋壓機帶來的問題更加突出。要是把小型工件放在大型旋壓機上加工,不僅是“大材小用”造成浪費,而且由于龐大笨重的設備控制、調整不靈,使加工精度降低,設備部件體積大,會互相爭奪空間,使施輪角度調節(jié)困難,甚至加工不出某些小徑半球形件,需要把旋壓機的一些部件作大調整才行。因此,一臺設備上勉強遷就就地加工多種大小不同的工件會帶來不少技術和經濟上的問題。較合理的辦法是將它們分別在幾臺設備上加工。
因此,在自動旋壓機設備總體布局的方案設計時,應按所加工的具體對像,處理好設備的加工適應范圍的寬窄關系。并對自動旋壓機設備布局和結構方案的先進性與經濟性相比較,進行取舍。
3.自動旋壓機適應不同控制系統(tǒng)的要求
對于采用一般半自動或程控系統(tǒng)的通用型旋壓機,多將旋輪座設計成可轉角調整的結構,既能滿足各種工藝要求,又能收到結構緊湊的效果。然而,對于同類的一些計算機數(shù)控的旋壓機,由于考慮到雙旋輪的同步精度難以控制和坐標系需要換算導致編程麻煩等原因,因此現(xiàn)在設計的數(shù)控旋壓機的旋輪座的縱向滑架與主軸軸線平行放置,并保持距離相等。而旋輪對工件所需的攻角,則通過設計旋輪頭特定安裝角或具有隨意調節(jié)攻角的機構等方法來解決。由此可見,控制方式的不同,也將影響到旋壓機的總體布局,也就是說,旋壓機的布局要適應于不同控制方式的要求。
4.保證自動旋壓機的加工質量
在考慮自動旋壓機的布局形式時,還應盡可能提高旋壓機的精度、剛度、抗振和耐磨等方面性能,以提高旋壓件的加工質量。在提高旋壓機的加工精度方面,除了可采取提高旋壓機零部件的制造和裝配精度外,還可以采取一些其他的方式,其中也包括合理布局。例如,多旋輪的采用相對主軸軸線對稱(等分)布置,在它們同時參與工作時,以平衡徑向旋壓力,提高主軸剛度。其次可把旋輪架設計成閉式框架(門式)結構,使其內力平衡,剛性大。另外,可盡量設法降低中心高度,并使橫向和縱向的進給力施加在與旋壓力同一個平面上,以減小旋輪架的傾倒力矩等,這些措施都有助于提高加工件的質量。
在考慮旋壓機的布局時,如根據(jù)“移輕就重”的原則,即較重的部件或芯模和工件造成固定不動,而移動較輕的部件以適應加工要求,一般可以同時改善前述的提高精度、剛度、抗振和耐磨等方面的性能。同時也可使所設計的旋壓機尺寸較小、重量較輕和結構較為簡單。
5.自動旋壓機應簡化結構、縮短傳動路線
在布局方面如能設法使傳動路線較短,通常也就容易使機構簡化。顯然,機構簡單和傳動路線短不僅容易制造,而且能夠降低成本,更重要的是還可以提高精度和便于操作。例如主軸傳動采用直流電動機或油馬驅動,只需少數(shù)幾級和幾擋齒輪傳動配合,既可實現(xiàn)無級調速,又可大大簡化一般的多級多擋的齒輪變速箱結構,還可通過電位計或節(jié)流閥來調節(jié)速度,故操作方便。又如旋輪架中的縱向進給采用油缸傳動,顯然結構大為簡化。
6.自動旋壓機應便于操作、調整、維護和檢修
自動旋壓機的布局還應適于操作者的操作習慣和操作方便的位置。例如臥式單旋輪的自動旋壓機,一般都把主軸裝置置于操作者的左邊,尾座置于右邊,如同車床一樣,都是為了適應于人們右手操作的習慣。至于雙旋輪的也是同樣道理,多數(shù)以前旋輪架(由尾座往主軸箱方向視為左的)為主,以后(右)旋輪架為輔。也就是說,電氣、液壓系統(tǒng)均以左邊旋架為主,當采用單旋輪工件時,也是用主旋輪架。此外一般使安裝工件和芯模等工具的部位高度設在1 M左右,為了適應操作者身材的高低和操作方便。當旋壓機較低時應該用床臺(腿)墊高。對較高的大型旋壓機就應該附設相應的操作踏板或工作架。裝卸工件、調整和換置機構及電氣操縱箱等都應布置在容易到達的地方,而且最好把這些機構集中在一定的區(qū)域,此外還應能在調整的同時便于觀察加工情況。從維護檢修觀點看,如能把旋壓機設計成幾個單獨部件的組合,而且各部的敞開性較好的結構布局,就較為方便。
7.自動旋壓機便于制造、占地面積小和考慮可否能納入自動線上工作
如果旋壓機的布局是便于維護檢修的,一般說來也就容易制造。并有降低成本的可能。在布局上還應該盡可能縮小占地面積。對自動化程度較高和多工序的自動旋壓機布局設計時,應兼顧考慮長遠使用的可能,即將這些旋壓機經過若干適當?shù)母难b后納入自動線上使用的可能。對于立式旋壓機,因這方面優(yōu)點更突出,故更應予以考慮。
除上述7點以外,在自動旋壓機布局的總體設計時,還應適當考慮設備外形,即要避免片面地追求美觀,也不應該忽視旋壓機外形對工作環(huán)境的美感作用,以免導致對勞動生產率產生不利的影響。為此,應注意將其外形輪廓線設計由直線或光滑的曲線組成,這樣較為悅目,而不規(guī)則的波折線會使人有雜亂的感覺。其次,要求各部件之間或部件對整個設備在形狀上應調和、勻稱,穩(wěn)定而安全,并能達到經濟和美觀大方的效果。
r系列羅茨鼓風機 羅茨鼓風機檢修作業(yè) 養(yǎng)殖用羅茨鼓風機價格 羅茨鼓風機間隙調整
山東錦工有限公司
地址:山東省章丘市經濟開發(fā)區(qū)
電話:0531-83825699
傳真:0531-83211205
24小時銷售服務電話:15066131928
